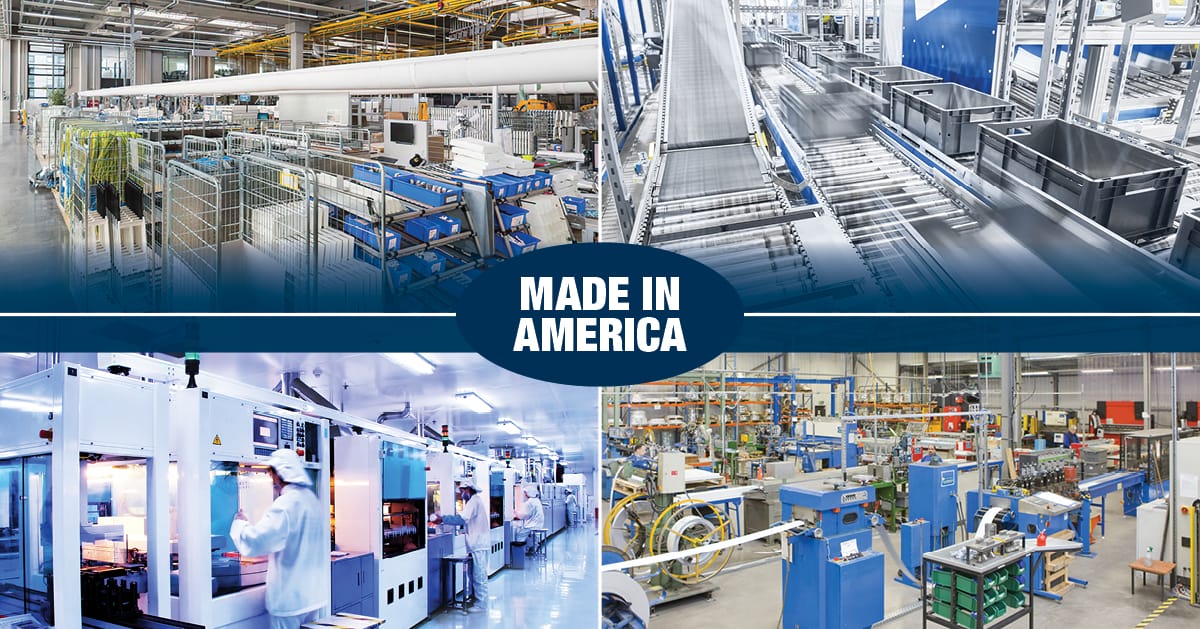
One of the pandemic’s inadvertent silver linings was that it exposed the fragility of the global supply chain. Worldwide shutdowns of manufacturing and distribution facilities disrupted the flow of goods. Everything from meat to toilet paper disappeared from grocery store shelves, and products manufactured overseas, like medical supplies, appliances, and microchips, were back-ordered for months.
Bringing Manufacturing Home
In response, many North American companies began to rethink their manufacturing strategies. While they could get their products manufactured more cheaply overseas, the uncertainty for timely product delivery accelerated the trend of relocating manufacturing operations to North America (“reshoring”). A December 2023 analysis of multiple surveys by the manufacturing magazine Assembly indicated that as much as 91% of U.S. manufacturers had reshored some production in 2022, up from just 7% in 2012.
A report published in the spring by the NAIOP Research Foundation found that pandemic-related supply chain disruptions and continued trade tensions between China and the United States, combined with the massive incentives offered by the federal government in the CHIPS Act, Inflation Reduction Act and Infrastructure Investment and Jobs Act made the moves even more attractive. Approximately 300 major manufacturing projects have been announced since 2020, collectively representing about 250 million square feet in aggregate to date, and that doesn’t include half of the projects that have yet to announce the details for their projects. The report estimates that the projects could increase the size of the U.S. manufacturing building stock by 6–13% within a decade.
In addition, numerous American companies are also “nearshoring” — establishing manufacturing operations in Mexico. This strategy not only brings operations closer to U.S. markets but also balances cost savings and provides greater control over the production process.
“This trend was already in place before COVID happened, and the pandemic accelerated the trend,” says Chris Drzyzga, VP/Partner with Voit Real Estate Services. “Reshoring is coming fast and furious out of the gates. There are some major projects underway throughout the port cities in the U.S. and Mexico. I see it as a major boon to not just the commercial real estate industry but the broader economy over the next 10 to 20 years.”
Drzyzga says the benefits for companies that are reshoring are myriad, from lowering the overall cost of production and distribution for the suppliers, enhanced control over the supply chain, and adding a “tremendous” number of jobs and overall economic activity to the regions and micro markets that have historically had a difficult time competing in the global economy. But he also cautions that the fruits of the reshoring plans will take some time to materialize. “You’re talking about a rather long pipeline here,” he says, “particularly for some of the chip, green energy, and electric vehicle plants throughout the U.S.”
Impact on Southern California Markets
So, what does this mean for the SoCal Industrial markets?
Although vacancy rates in the Southern California markets tracked by VOIT have essentially doubled year over year, they remain relatively low — ranging from 4.18% in Orange County to 6.76% in the Inland Empire in Q2. Sublease space has driven availability rates up to 7% or 8% in most markets, with the Inland Empire’s 11.1% an outlier. Space is still fairly tight, so there aren’t many opportunities for developers of large-scale manufacturing facilities to enter the market.
However, Drzyzga believes there is currently a window of opportunity for owners of smaller industrial facilities under 50,000 square feet to capitalize on a supply-constrained market at record valuations. Those who choose to hold their assets long-term will need to plan on making significant investments in the assets to ensure they remain relevant and competitive.
“Next-gen business models are a part of this, but more importantly, over the next five to ten years, regulations are going into effect at the state level in California — some already have — that are going to increase investment costs and the cost of doing business,” he explains. Chris cites regulations such as Title 24 (designed to fulfill California’s goal of running entirely on renewable energy by 2045), additional commercial building taxes, and changes to planning, permitting, and labor laws. “Over time, as newer facilities get built out and the economy evolves, the existing inventory of pre-1990 and older industrial buildings will become functionally and economically obsolete. If a building has 20-foot clear or less, if it’s got funky angles or configurations, or if the power loads are under 600 amps, all of those things are going to contribute to a lack of relevance and competitiveness in the market. And the cost of improving them is going to far outweigh the future returns, so it will make for a very simple decision for some of these folks because the numbers just won’t pencil.”
Nearshoring Proving Boon for American Companies
American companies are also reaping the benefits of nearshoring, often gaining shorter, more flexible supply chains and access to a talented labor pool. Last year, Mexico surpassed mainland China as the largest exporter to the U.S. According to a report by global management consulting firm Kearney, U.S. imports of Mexican manufacturing goods grew from $320 billion to $422 billion (32%) since pre-COVID days. Imports from Canada have also steadily increased since the pandemic.
The pandemic has reshaped the industrial landscape across North America through reshoring and nearshoring. Southern California’s industrial market will continue evolving to meet the needs of manufacturing entities seeking to relocate to the region or nearby locations in Mexico.
To learn more about the industrial markets in Southern California, check out our market reports for the Inland Empire, Los Angeles, Orange County, Mid Counties, and San Diego markets. Talk with one of Voit Real Estate Services’ trusted commercial real estate advisors to learn how reshoring and nearshoring affect your industrial investments.